Fluid Mechanics Ltd has invented a technology that improves the energy efficiency of heat pumps by 50% or more while eliminating the need to use gases with a high global warming potential
The global use of heat pumps
Heat pumps are widely used globally for space heating, air conditioning and refrigeration. They are the single biggest load connected to the electrical grid, and in the coming years their use will continue to grow as the switch is made from gas fuel space heating to ground and air source heat pumps. In the transport sector they are widely used for refrigerated transport and shipping; most vehicles sold today also have air conditioning fitted as standard.
The problem
Today nearly all heat pumps use a technology called the vapour compressor. Vapour compressor heat pumps were invented in about 1850. Even the most efficient vapour compressor heat pumps are not very efficient compared to the theoretical maximum defined in thermodynamics by the Carnot cycle. The best vapour compressor heat pumps are about 40% efficient compared to Carnot (for cooling) and often as low as 10%, particularly when operating away from the optimal duty point. Currently there are no practical alternatives to the vapour compressor cycle for most applications.
Innovative solution
Significant improvements in energy efficiency
Fluid Mechanics has applied its near-isothermal technology to an existing heat pump cycle called the Stirling cycle. The Stirling cycle is well established and can be used for both heat engines and heat pumps. Currently the Stirling cycle only has niche heat pump applications such as cryocoolers (producing liquid nitrogen from air). By applying the near isothermal technology to the Stirling cycle, it is possible to make a heat pump which has similar heating/cooling capacity to the vapour compressor cycle while being significantly more energy efficient. Fluid Mechanics’ system is demonstrating potential efficiencies up to 75%, although in a practical machine efficiencies of between 50 to 60% of Carnot are expected.
Global warming benefits
In addition to the energy efficiency advantage, the preferred operating gas inside the Near-Isothermal Stirling machine is helium or hydrogen. These gasses have zero GWP (global warming potential) compared to CO2. The vapour compressor cycle generally uses HFCs gasses with a GWP of c.5,000. The Kigali Amendment to the Montreal Protocol mandates an 80% reduction in these harmful gasses, this is causing much upheaval in the industry. The Near Isothermal Stirling Heat Pump provides a simple solution to this problem.
Current status
Fluid Mechanics has built working prototypes to demonstrate and prove the technology. It has patent protection on the core technology and has several further patents planned.
The Crowley Heat Pump
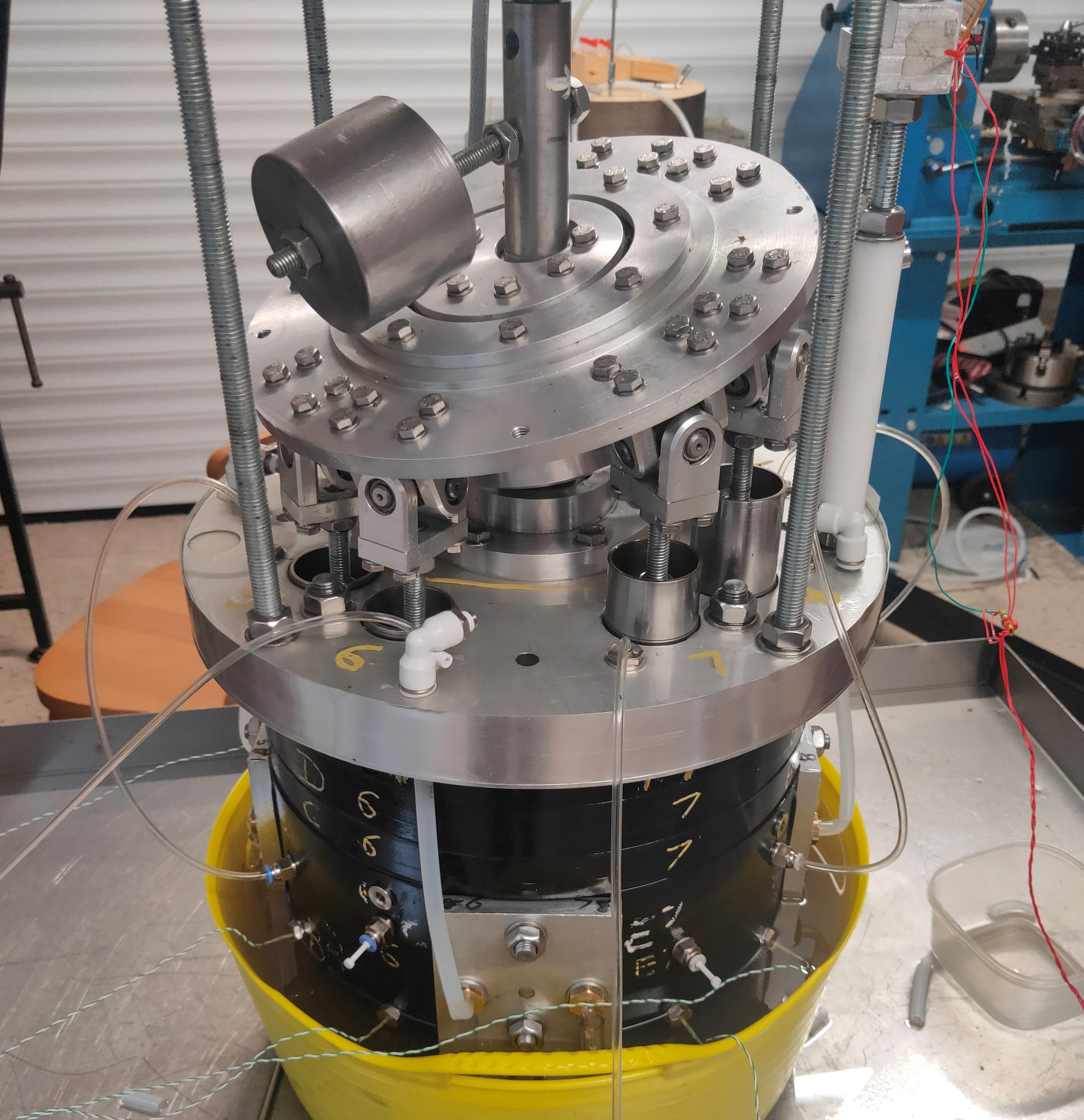
Prototype Near-Isothermal Stirling Heat Pump
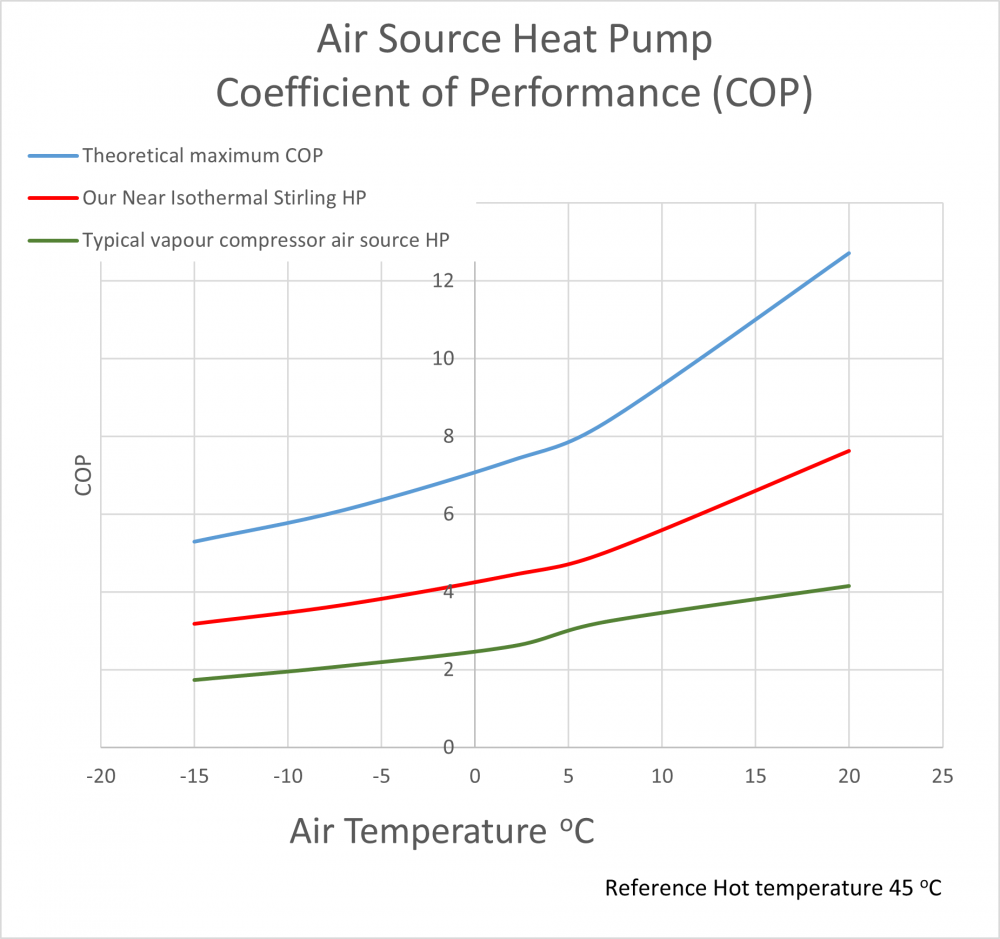
For air source heat pumps the COP (coefficient of Performance) is the ratio of output heat compared to input power. So, for example if the COP is 3, for every 1kW of electrical input power, 3kW of heat are provided. The extra 2kW of heat is heat extracted from the external air.
The COP for an air source heat pump is not fixed. It depends on the temperature difference between the external air and water, the lower the temperature difference the higher the COP and system efficiency. Air source heat pumps provide hot water at a range of temperatures. In the chart a single hot water delivery temperature of 45oC has been chosen to compare the typical performances of the vapour compressor heat pump (green line), the expected performance of the near isothermal Stirling heat pump (red line) and the theoretical maximum performance defined by Carnot (blue line).
So, for example when the external temperature is -5 oC the existing technology will provide a COP of 2.1, the near isothermal heat pump will be 3.8 and the theoretical maximum is 6.4.
Dec 2020